Metallisierte Polymerfolien als Stromkollektor
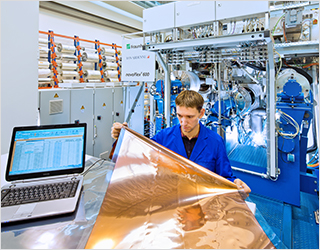
Anwendung
Metallisierte Polymerfolien als Stromkollektoren bieten gegenüber den bisher verwendeten Metallfolien interessante Angriffspunkte um sowohl die gravimetrische als auch die volumetrische Energiedichte zu erhöhen und gleichzeitig Sicherheitsaspekte der Batterie zu verbessern und knappe Ressourcen einzusparen.
- Dünne und leichte Stromkollektoren zur Steigerung der volumetrischen und gravimetrischen Energiedichte
- Ersatz von Metallfolien durch metallisierte Polymerfolien
Entwicklungsparameter
- Foliendicke (Grundsubstrat) < 8 µm
- Metalldicke > 1 µm
- Gesamtdicke < 10 µm
Technologie
- Rolle-zu-Rolle Prozess für Folienbreiten > 400 mm und Bandlängen > 100 m
- Doppelseitenbeschichtung mit Al oder Cu mittels
- Elektronenstrahlverdampfung
- Kathodenzerstäubung (magnetron sputtering)
Vorteile
- Gewicht, Dicke
- Erhöhung der intrinsischen Sicherheit von Batteriezellen