Metallized polymer films as current collector
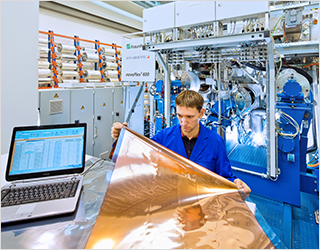
Application
Metallized polymer films as current collectors represent interesting opportunities to increase both gravimetric and volumetric energy density while improving battery safety aspects and saving scarce resources compared to previously used metal films.
- Thin and lightweight current collectors to increase volumetric and gravimetric energy density
- Replacement of metal foils by metallized polymer foils
Development Parameters
- Film thickness (base substrate) < 8 µm
- Metal thickness > 1 µm
- Total thickness < 10 µm
Technology
- Roll-to-roll process for film widths > 400 mm and strip lengths > 100 m
- Double side coating with Al or Cu by means of
- electron beam evaporation
- cathode sputtering (magnetron sputtering)
Advantages
- Weight, thickness
- Increasing the intrinsic safety of battery cells